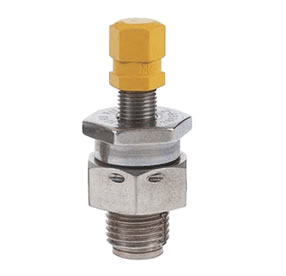
High-pressure shock strut valves play an important role in many aircraft landing gear systems. Like with other valves, they are designed to control the flow of substances. While other valves control fluids, though, high-pressure shock strut valves control gas or air. What are high-pressure shock strut valves exactly, and how do they work?
Overview of High-Pressure Shock Strut Valves
High-pressure shock strut valves are devices that regulate the pressure in shock struts. They are a common component of aircraft landing gear systems, specifically shock struts.
Also known as oleo struts, shock struts use pressurized gas — usually nitrogen gas — and hydraulic fluid to dampen shock loads. When an airplane lands, the shock struts will absorb and dissipate the impact so that the airframe is exposed to less stress. The end result is a smoother, safer landing.
How High-Pressure Shock Strut Valves Work
High-pressure strut valves work by regulating the flow of pressurized gas and fluid. Shock struts require a specific operating pressure. They are filled with gas and hydraulic fluid, which creates pressure inside of the shock struts.
If the pressure is too low, however, the shock struts may fail to adequately dampen the shock of landings. If the pressure is too high, on the other hand, it will jeopardize the integrity of the shock struts. Excessively high pressure may cause various components of the shock struts to fail and eventually leak. Therefore, shock struts are often used in conjunction with valves to regulate their internal pressure.
Most high-pressure shock strut valves consist of three parts:
- Valve body: the main body or structure
- Flow control mechanism: regulates the flow of gas and fluid
- Seal assembly: seals the valve body and flow control mechanism to prevent leaks
While there are different types of high-pressure shock strut valves, most of them are designed to work automatically. When landing, shock struts will compress. This compression will result in less space inside of the shock struts, thereby increasing their internal pressure. Shock strut valves control the flow of fluid in shock struts while simultaneously ensuring that the internal pressure is right.
Understanding Operating Pressure
All high-pressure shock strut valves have a specific pressure for which they are rated to operate. Known as the operating pressure, it determines how much gas and fluid the valves will allow to flow through them.
You should choose a high-pressure shock strut valve with an operating pressure that matches that of the shock struts with which you intend to use it. Some high-pressure shock strut valves are rated for 5,000 pounds per square inch (PSI). If you’re working on an airplane with 5,000-PSI shock struts, for instance, you should choose these valves.